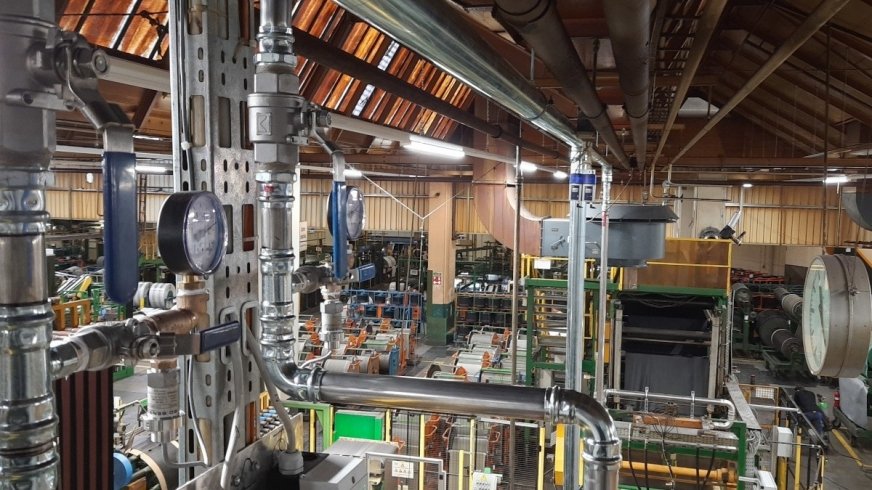
Kord. Opony diagonalne i radialne.
W oponach radialnych włókna są umieszczone względem siebie równolegle i nie przeplatają się ze sobą, dzięki czemu opony są w stanie bardziej uginać się na bokach. Opona radialna (inaczej promieniowa) jest dziś standardem konstrukcyjnym w branży, szczególnie jeśli chodzi o opony osobowe.
Dziś? Praktycznie tylko w rolnictwie i w branżach pokrewnych diagonalne ogumienie trzyma się mocno. I nic dziwnego, skoro technologia diagonalna jest starsza od radialnej. Opona diagonalna jest stosowana w przemyśle motoryzacyjnym od samego początku (1898 rok uznaje się za moment, kiedy zastąpiła opony z pełnej gumy w pojazdach do transportu drogowego). Przed wprowadzeniem radialnych odpowiedników w późnych latach 40 XX wieku, diagonalna opona była niejakim standardem w branży oponiarskiej.
Nie wdając się w szczegóły, promieniowe ustawienie włókien zapewnia dodatkową stabilność. Warstwa ta wpływa przede wszystkim na nośność opony, a także na zachowanie zawieszenia i właściwości jezdne.
Próżnia osiągana? To pytanie o: ilość potrzebnej energii
W przemyśle oponiarskim, technologia próżniowa jest stosowana do obsługi zadań przy maszynie do cięcia tekstyliów. Jak to wygląda? W zaawansowanym cyklu produkcyjnym gumowana siatka jest przycinana na żądaną długość, a następnie bezpośrednio nakładana na inny pasek za pomocą maszyny podnoszącej i przenoszącej. Wytwarzanie próżni (w elementach przyssawek) w maszynach CNC może generować pokaźne straty energii, skoro precyzyjne pozycjonowanie jest najważniejszym aspektem jakości gotowej siatki tekstylnej. Poszczególne warstwy muszą przecież leżeć dokładnie - jedna na drugiej.
Jak ograniczyć zużycie energii zasilającej ciąg produkcyjny? Do niedawna ratowano się rozwiązaniem bardzo energochłonnym. Przykładowo, Continental Reifen Deutschland GmbH produkuje wysokiej jakości opony do samochodów osobowych i dostawczych w swoim zakładzie produkcyjnym w Aachen w Niemczech, gdzie do niedawna jedna dmuchawa boczno-kanałowa była stosowana w każdej z trzech maszyn do cięcia tekstyliów. Takie właśnie dmuchawy zapewniały próżnię niezbędną do pracy z taśmami tekstylnymi. Dmuchawy pracowały stale z pełną mocą, zużywając w ten sposób ogromne ilości energii. Dodatkowo powodowały znaczny hałas – bardzo uciążliwy dla pracowników zaangażowanych w procesy produkcyjne.
Dość powiedzieć, że dmuchawy boczno-kanałowe generowały hałas na poziomie 94 dB. Do czasu, gdy rok temu jeden z pracowników Continental Reifen, po prostu… nie wytrzymał i zasugerował za pośrednictwem wewnętrznego działu zarządzania pomysłami, by ktoś „przysłuchał się bliżej” decybelom w sąsiedztwie maszyn do cięcia tekstyliów.
Komentarze (0)